Client Background
US-based global heavy vehicle and lifting equipment manufacturer with large UK factory that manufactures several product ranges shipped around the world.
Client Brief
Our client developed a new all-electric range to complement their existing people lifting vehicle ranges. They expect this new range to be one of their top sellers as they will sell it through their global sales channels with the main target markets being in Europe and North America.
They needed a partner-supplier that could support the prototyping/design requirements including new critical tolerances and Quality Assurance requirements, and then scale the production in line with their sales plans.
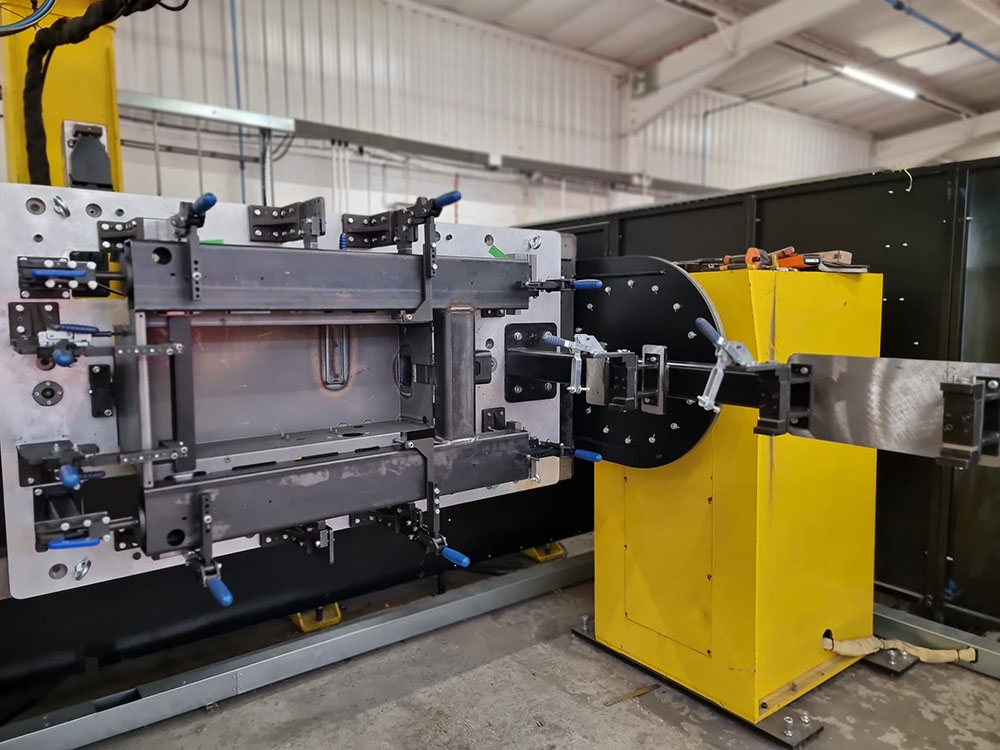
Gantry-Driven MIG Robot Welding System
A key part of our support was investing in a new gantry-driven MIG robot welding system, so that welding requirements could be maintained as the monthly number of fabricated chassis increases from 30-40 to +60qty a month over the next year.
Why choose CEL for MIG robotic welding
Our client has a number of metal fabrication suppliers. They chose CEL as we have successfully worked with their Engineering and Quality Assurance teams on a number of smaller parts and fabrications with strong results. We also have the MIG robotic welding skillset and capacity to grow with their requirements.
We achieved their rigorous Level II Production Part Approval Process (PPAP) and Advanced Product Quality Planning (APQP) requirements.
Early on we identified that in order to scale our production with theirs’, we would need to invest in robotic welding to remove welding as a future bottleneck. We started discussions with our systems integrator so that the robotic system and assembly fixtures would in-process as we moved to production runs.
Initial CEL Support
One of the early challenges was working with our client’s Engineering and Quality teams on setting tolerances that included tolerances withing the various box section and machined parts that we sourced through our supply chain.
These material tolerances needed to be incorporated into the welding and fabrication tolerances and the requirements of the final product. We had an open discussion that included 8-D quality problem solving methodology to isolate issues, discuss amongst the team and develop solutions.
CEL Solution
We worked through several design changes and tolerance adjustment so that the fabrication would accommodate the other mechanical electrical and machined parts that make a fully assembled product
This product range is one of our clients’ most important ranges as it is now being sold in Europe and North America. Our partnership approach focused on Quality Assurance and Supply Chain Integration helped give our client the confidence to count on Contracts Engineering to deliver to their requirements.
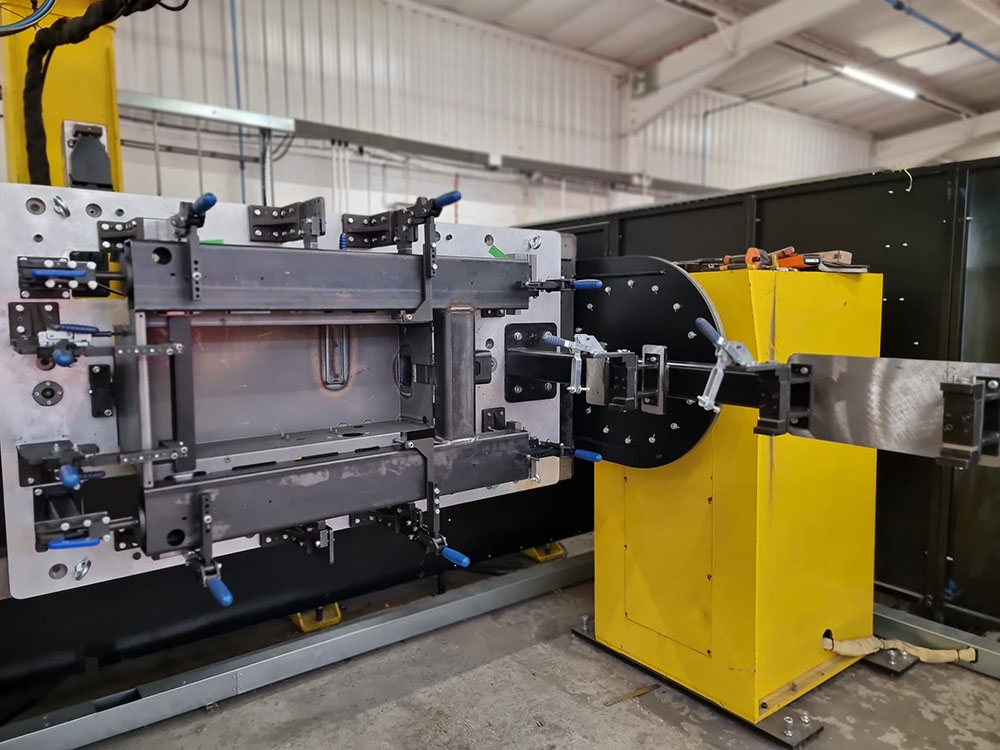
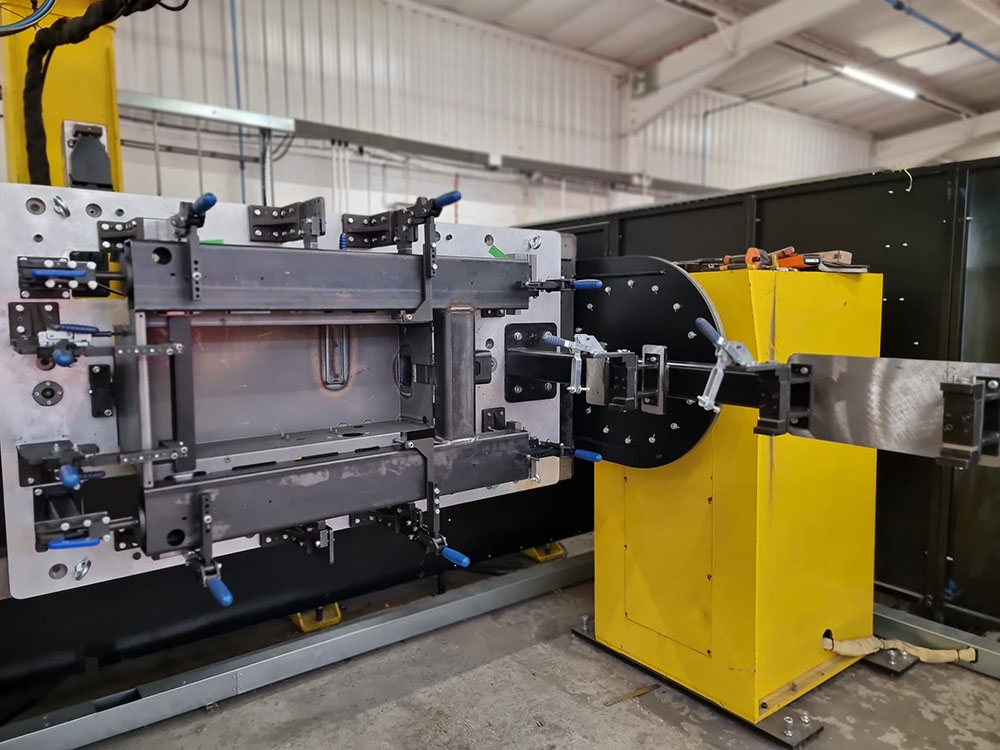
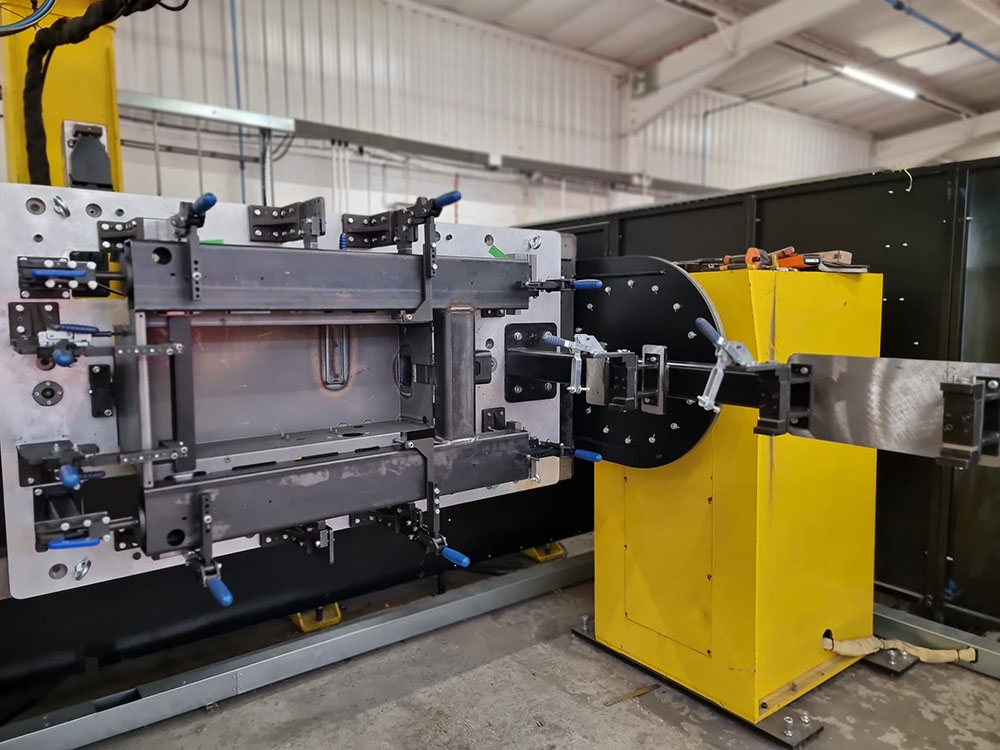
Contracts Engineering has been a metalwork supplier for a few years now and this chassis relaunch project has been an important part of our growth plan. We knew we could count on CEL to deliver and we are happy to have them as one of our key suppliers.